Types of Welding Joints: An In-Depth Guide
Understanding the different types of welding joints is crucial for anyone involved in welding, metal fabrication, or structural engineering. The right welding joint can influence the strength, stability, and aesthetics of your project. This SEO-optimized blog will delve into the most common welding joints: Butt Joint, Tee Joint, Corner Joint, Lap Joint, and Edge Joint. Whether you’re a professional welder or a DIY enthusiast, this guide will provide valuable insights into choosing and implementing the correct welding joint for your specific needs.
Butt Joint
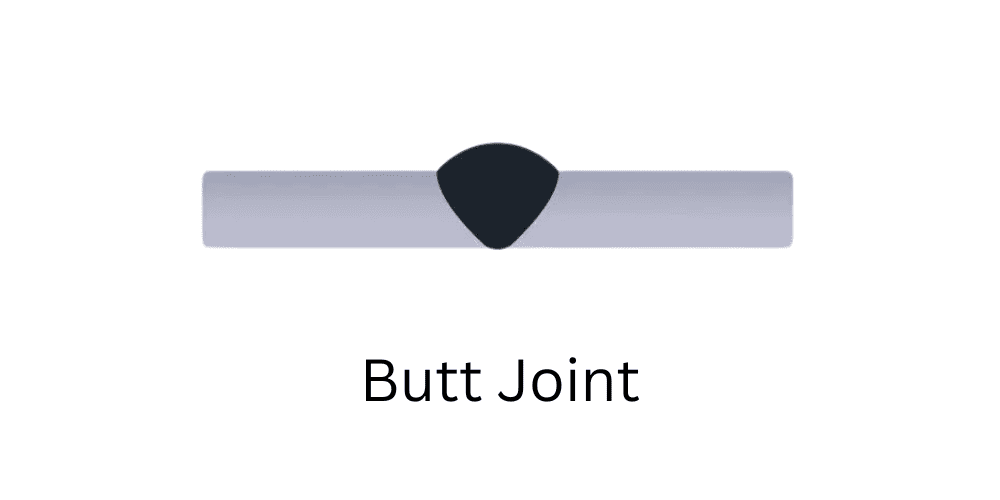
A Butt Joint is one of the simplest and most commonly used welding joints. It involves two pieces of metal that are placed edge-to-edge and welded along the seam. Here’s what you need to know:
- Applications: Suitable for joining plates, sheets, and structural components.
- Advantages: Provides a strong and straightforward weld, ideal for simple assemblies.
- Disadvantages: Requires precise alignment and preparation to ensure a quality weld.
- Common Uses: Structural components, pipe connections, and simple metal fabrications.
Tee Joint
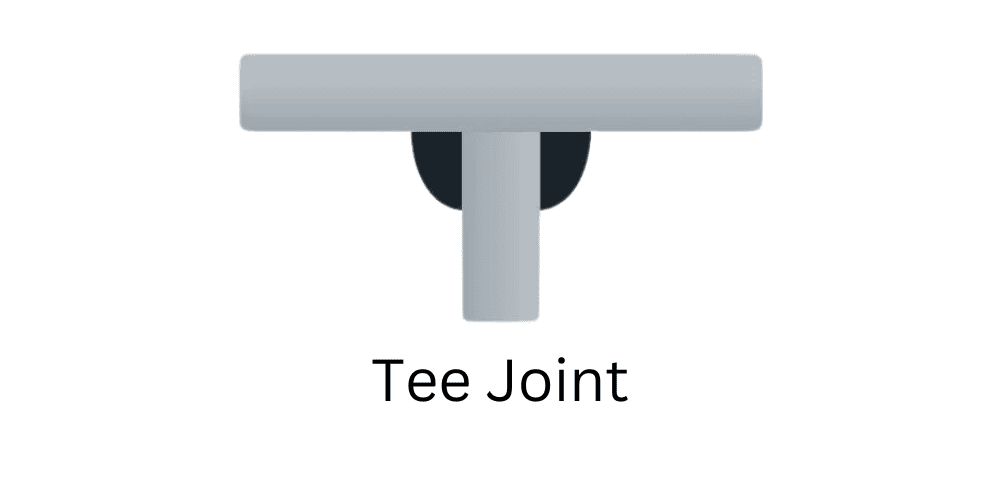
A Tee Joint is formed when the edge of one piece of metal is welded to the surface of another piece at a right angle, creating a “T” shape. Key characteristics include:
- Configuration: One metal piece is perpendicular to the other, forming a 90-degree angle.
- Applications: Often used in constructing frames, supports, and stiffeners.
- Advantages: Provides good mechanical strength and load-bearing capacity.
- Disadvantages: May require additional support or fixtures to maintain alignment during welding.
- Common Uses: Structural frameworks, industrial supports, and reinforcing elements.
Corner Joint
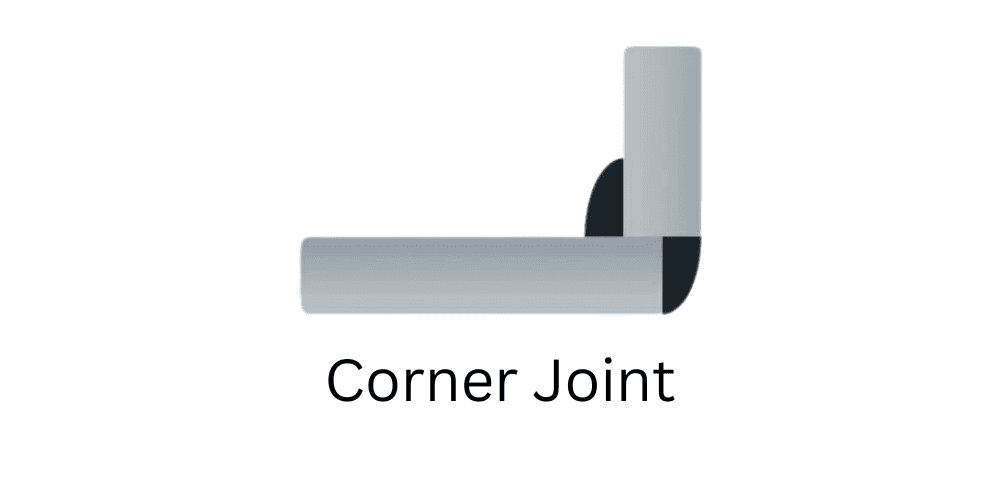
A Corner Joint involves welding two metal pieces together at their corners, forming a right angle. It is commonly used in box or frame constructions.
- Configuration: The edges of the metal pieces are joined to form a corner.
- Applications: Ideal for making frames, boxes, and enclosures.
- Advantages: Provides good structural integrity and is relatively easy to align.
- Disadvantages: May be susceptible to distortion or warping if not properly supported.
- Common Uses: Metal boxes, frames, and sheet metal constructions.
Lap Joint
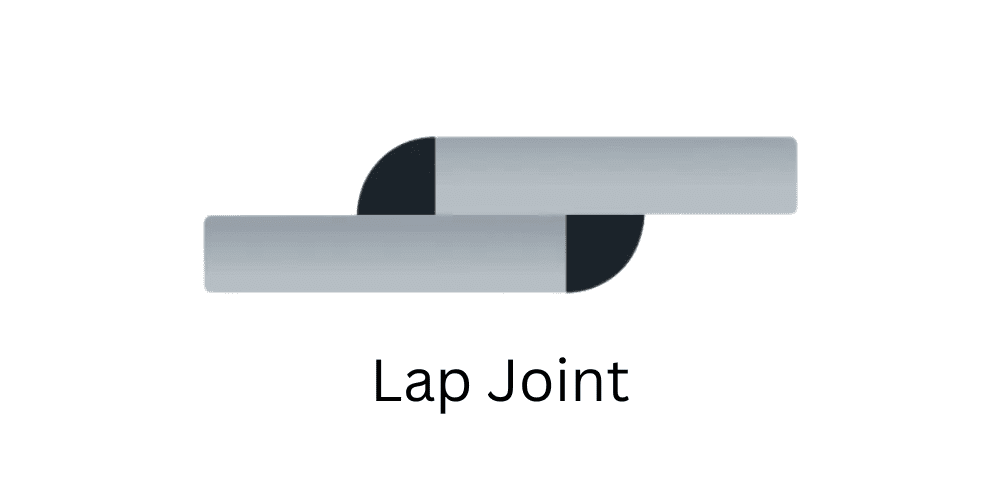
A Lap Joint is created by overlapping two pieces of metal and welding along the edges. This type of joint is useful for joining thin materials.
- Configuration: One metal piece overlaps the other, and the weld is applied along the edge.
- Applications: Common in sheet metal work and situations where butt joints are impractical.
- Advantages: Provides a larger surface area for welding, increasing joint strength.
- Disadvantages: May create stress concentrations and is not ideal for thick materials.
- Common Uses: Sheet metal assemblies, automotive panels, and thin material joints.
Edge Joint
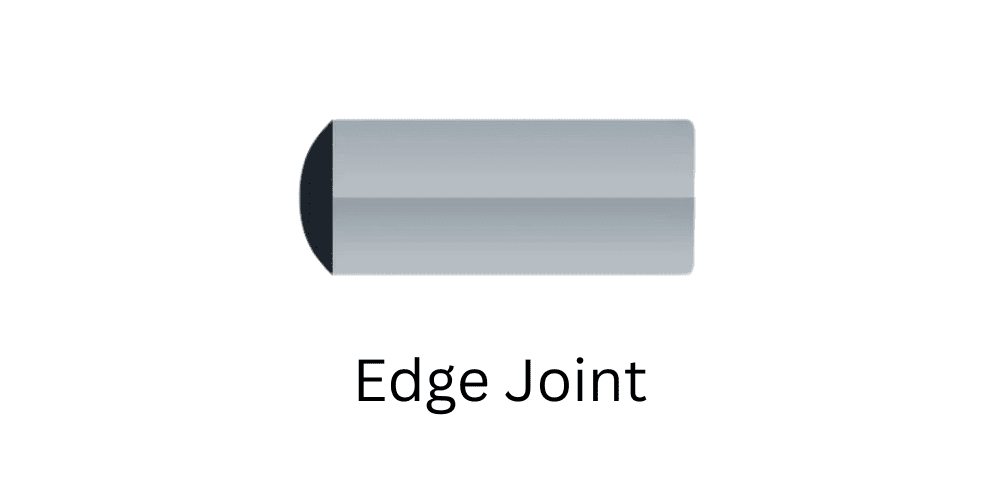
An Edge Joint involves welding the edges of two or more metal pieces that are placed side by side. This joint is often used when pieces are joined to form a surface.
- Configuration: The edges of the metal pieces are aligned and welded together.
- Applications: Suitable for joining thin materials and sheet metal.
- Advantages: Provides a clean, continuous weld seam along the edges.
- Disadvantages: Limited strength and not suitable for high-stress applications.
- Common Uses: Sheet metal fabrication, tanks, and joining flanges.
Choosing the Right Welding Joint
Selecting the appropriate welding joint depends on several factors, including the materials you are working with, the type of project, and the desired strength of the weld. Here’s a quick guide:
- For general-purpose welding: Butt joints are straightforward and strong.
- For framing and structural support: Tee joints and corner joints provide good load-bearing capacity.
- For sheet metal work: Lap joints offer a simple way to join thin materials.
- For creating surfaces: Edge joints are ideal for making continuous seams along edges.
North Perth’s Trusted Welding Services
Looking for professional welding services in North Perth and surrounding areas? Contact AttachPro Welding for expert solutions and reliable support. Discover how our expertise in various welding joints can help you achieve the best results for your metalwork projects! Contact us today to learn more about how we can assist with your welding and fabrication projects!